New Clutch
This info is not comprehensive.
The clutch outter is the clutch basket.
CAUTION
- Try to use a good quality socket to remove the
crankcase cover bolts as anything less may result
in you rounding off the heads of the bolts.
- Once you have the bolts removed, the crankcase
cover will still be stuck onto the crankcase,
Do not attempt to lever off the cover by inserting
anything under the cover because any damage to the
mating surfaces will result in oil leaks later.
There are "ears" on the crankcase cover that can be
used to remove it.
- The clutch pressure plate is made of very weak
aluminium and is very easy to break. Loosen the
bolts in a criss cross pattern and do not tighten
the bolts too hard.
- When removing the old gasket be carefull not to
damage the mating surfaces of the crankcase cover.
- Before you tighten down the four lifter plate
bolts be sure that the springs are pressing all the
friction plates and steel plates together.
- Do not allow any foreign particles to enter the
crank case while you have the cover removed.
- Soak the new clutch friction plates in fresh
motor oil for several hours before fitting. Also
coat the steel plates in motor oil before fitting.
What you need
- Full set of friction plates.
- Four springs.
- Clutch lock nut.
- Clutch cover gasket.
- You may need new steel plates if the old ones
are scored or warped (unlikely).
Tools
- 8mm, 10mm and 27mm sockets.
- Tools to clean gasket mating surfaces.
- Something to unstake the clutch lock nut.
- Feeler gauge.
- Vernier caliper.
- Torque wrench
- Breaker bar and 27mm socket.
- Clutch center holder, You could avoid needing
this tool if you just put the bike into gear.
Procedure
- Remove the exhaust down pipe of the rear
cylinder (you will need a long extension for
your rachet to do this). Romove the bolt that
secures the exhaust collector box to the right
foot rest hanger so that the collector box will
drop down 1 or 2 mm which will make it easier
to remove and install the down pipe.
- Remove the crankcase cover bolts in a
criss cross pattern.
- Use the "ears" on the cover to remove
it from the engine.
- Before you remove the clutch unit test
the damper. There is a large metal gear
rivetted to the back of the clutch basket.
There is a damper between the gear and the
basket much like the damper behind the rear
sprocket. The strength of two hands should
not be able to rotate the damper, if there
is free movement then the basket is defective.
- Carefully remove the four spring
loaded lifter plate bolts, turn each bolt
a quater a turn at a time, in a criss cross
pattern, maintain equal pressure on each bolt.
Once the bolts are half way out you can remove
them quicker.
- Romove the lifter plate and springs.
- Before you remove the clutch center lock nut note
how the four colums of the pressure plate feel loose.
- Unstake and remove the clutch lock nut
(27mm socket with breaker bar and extension),
use the clutch center holder to hold the clutch
unit OR put the bike into 5th gear and press the
rear brake to stop the clutch unit form turning.
Sometimes this nut is difficult to remove, an impact
wrench and a blow torch might help.
- Romove the clutch inner (The judder spring
and it's seat should be on this) Check for wear
where the steel plates press on the clutch inner.
- Remove the Friction plates and the steel
plates.
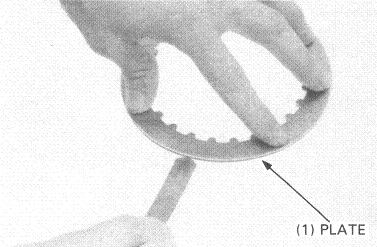
- Inspect the steel plates for scoring or
warpage, warpage service limit is 0.3mm.
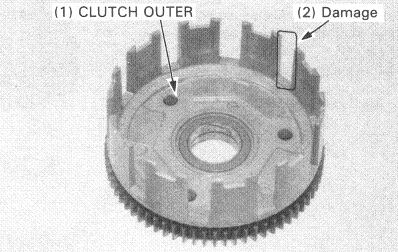
- Remove the pressure plate.
- Remove and inspect clutch outer for damage
or wear where the friction plate tabs press
on the basket.
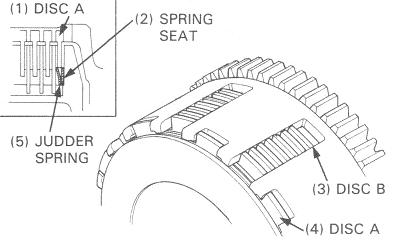
-
- Lay the clutch basket on you work bench
- Install the pressure plate
- Install a friction plate then a steel
plate then another friction plate etc.
NOTE: There should be one different friction
plate in your set , the one that is different
goes on last. The last friction plates tabs
go into a different slot that the other plates.
- Install the clutch inner, rotate it as
you push it in. Make sure it is all the way
in.
NOTE: the judder spring and it's seat should be
in place, look at picture to see how the
Judder spring is orientated.
- Install your assembled clutch unit onto it's
shaft.
NOTE: If the unit wont go on all the way then
move the oil pump chain to align the bosses
and then push it on.
- Double check that everything has seated.
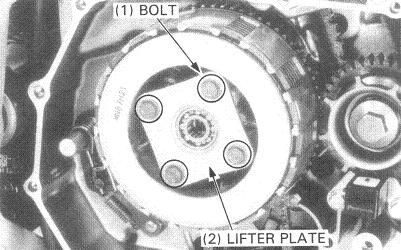
- Instal and tighten (130 Nm) and stake clutch
lock nut.
Note: Before you stake the lock nut check that
the four colums of the pressure plate feel loose
like they did before you removed the nut. If it's
not loose then something is catching and the nut
will have to be reomved.
- Install springs, lifter plate and the four
bolts, before you tighten down the bolts check
that the springs are pressing all the friction
plates and steel plates together. If the plates
are not being pressed together then the clutch
will not work and may break the pressure plate.
- Carefully tighten down the four lifter
plate bolts in a criss cross pattern, turning each
bolt 1/2 of a turn at a time, maintain equal spring
pressure on each bolt, do not tighten the bolts too hard
as this will break the pressure plate, Simply seat
the bolts and tighten them securely (guess: 10Nm).
Note: When the bolts are screwed all the way in they
should tighten suddenly, if they just tighter and tighter
then something might be wrong.
- Check that everthing has seated properly and
that the friction/steel plates are being pressed
together by the springs.
- Make sure the oil nipple, O ring and washer for
the cam oil feed pipe are in place.

- Apply liberal amounts of grease to crank case
mating surfaces and to the gasket.
- Check that the cluch lifter is seated properly
in the crankcase cover.
- Insert the dowel pins into the crank case then
apply the gasket followed by the crankcase cover.
- Tighten the crank case cover bolts in a criss
cross pattern.
- Install exhaust down pipe
- Apply copper grease to the threads of all bolts
or nuts.
Torque values:
8mm oil bolt on R crankcase cover |
23 Nm |
Crankcase cover bolts |
10 Nm |
Clutch lock nut |
130 Nm |